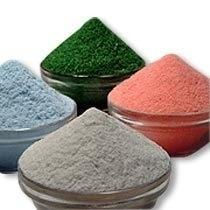
Foundry Chemicals Market Evolving with Foundry Owners Turning to 3D Sand Printing
The foundry industry, being in-line with Industry 4.0 trends, is making a move towards adopting technologically-advanced business operations, and 3D (3 dimensional) sand printing technology is revolutionizing the industrial landscape for manufacturers and suppliers in the foundry chemicals market space. An upsurge in the adoption of 3D sand printing technology is mainly attributed to its larger printing volumes as compared to any other conventional 3D printing technology, inexpensive printing materials, and its ability to print functional metal parts that are adjunct to metal powder used in the post processing of sand and metal castings. The foundry chemicals market is projected to increase at a CAGR of ~3%, to reach a value of ~US$ 2.9 Bn by 2027.
In recent times, innovative 3D binder technologies are being actively used for organic and inorganic sand printing for additive manufacturing processes. Manufacturers who seek print head compatibility, dimensional accuracy, and productivity are turning towards 3D sand printing to minimize labor-specific efforts and improve efficiency over conventional binders. This trend has seen a significant shift in manufacturers’ preference of producing metal-sand molds and robust concrete structures used for various applications in architecture and infrastructure industries.
For instance, in June 2019, ASK Chemicals, a leading foundry consumables company, announced the launch of INOTEC 3D ? a new-age 3D sand binder that uses printing fluids and promoters in high temperature curing additive manufacturing processes involved in the production of sand castings. This helps manufacturers produce complex-shaped industrial sand components, and combine multiple sand cores into one.
Automating Production of 3D-printed Cores Gains Stakeholders’ Attention
Foundry businesses have evolved from developing sand mixers, which were primarily used to produce mixed sand on demand, to using next-gen 3D printing technologies. Today, the global foundry chemicals market has become a ~US$ 2.2 billion landscape, excelling in printing technologies that can accelerate the production of 3D metal, sand prototypes, and various other critical components that are used in automotive, aerospace, petrochemical, and construction industries.
Stakeholders in the global foundry chemicals market are keen on expanding their product offerings for binders, additive agents, and coatings, so as to expand their foundry chemicals market share and product penetration applicable to various industries. Subsequently, efforts are being made to reinvent the manufacturing landscape in the production of core components and 3D printed units for various end-use industries. On the same lines, ASK Chemicals - a leading foundry consumables company, announced a collaboration with Loramendi & Aurrenak ? a leading group for the design and supply of solutions in core making, molding, and casting services, and Voxeljet - a leader for 3D printing systems, to pioneer the technique of additive manufacturing in foundry-serial production, backed with one-of-its kind technology for a fully-automated 3D printed core production solution. This technology allows the automated production of highly complex sand cores applicable in casting processes, by harnessing the flexibility that additive manufacturing provides and eliminates the issue of the design limitations of conventional tool technology.
Software Modernizations for Producing Iron and Steel Castings Build Future Business Avenues
In the foundry chemicals market, the demand for core and mold binders, sand additives, and parting agents in iron, steel, and aluminum foundries has always remained high. In addition to this, the demand for foundry chemicals triggered by iron and steel melt shops has led to cutting-edge innovations in spot feeders for pliable iron castings, SCK (Sleeve Construction Kit) for the spot feeding of heavy-duty iron and steel casting and heat-intensive feeders for aluminum casting. These innovations are adding value to manufacturers, as they provide benefits such as steel filtration combined with a novel shrouding system, unmatched levels of re-oxidation removal from metals, and drastic improvements in casting quality, as well as reduced rework.
Such innovations are also catalyzing the need for software and technological modernizations. As an example, Foseco-Vesuvius, a leader in the supply of foundry consumables and solutions, announced the launch of the newly developed Ferrolab V ? a thermal analysis system for iron foundries. This system is easy to run and install, and contributes to real savings due to reduced scrap volumes and the increased casting quality of iron and steel metals. Also, for aluminum foundries, Foseco-Vesuvius is planning to promote its latest development of SMARTT Melt Treatment Stations and Degassing units that facilitate enhanced hydrogen level control, value-worthy inclusion removal, and superior grain refining for aluminum casting.
Along with iron, steel, and aluminum transformations, Foseco is also focusing on leading-edge tech and software developments for automotive coatings that provide one of the optimum levels of internal casting cavity cleanliness in the foundry industry, and features alongside their latest generation of ANTICOTE coatings. This coating system consists of an Intelligent Coating Unit, which ensures consistent coating application, minimizes coating related scrap, and improvises productivity volumes in the core room.
Need for Environment-friendly Processes and Productivity Improvements Influence Market Trends
The adverse effects of casting operations by foundries is seen as one of the major concerns for environmental well-being. To meet the increasingly rigid carbon regulations formulated by various governments, companies are rethinking new alternatives of transforming their business operations required for long-term sustainability.
In an attempt to tackle this environmental issue, ASK introduced the MIRATEC TC technology to demonstrate its best performance in turbocharger casting. This state-of-the-art technology is used in the steel casting of zirconium-containing coatings, attributing to the efficient refractory properties of zirconium. This makes the technology an environmental-friendly alternative as a result of drastic reduction in the emission of carbon and hazardous gases, without affecting the functionality of the turbocharger.
However, challenges such as the need for new technologies and productivity improvements could act as restraints that may slow down the market growth of one of aluminum’s major domain that caters to the high pressure die casting. To avert these challenges, manufacturers are adopting the Vacuum Die Casting technology, which improves mold fitting for thin-walled components, and is apt for crash-relevant components used in automotive, rail vehicles, and construction industries.
Due to the rising demand for improved process reliability and quality pertaining to chassis and structural parts, stakeholders are also adopting the technique of minimal lubrication water consumption, which reduces wastewater scrap and increases the product lifecycle of molds.
Comentarios